As an important mobile device, industrial casters are widely used in various industrial scenarios. According to the different scenes of use, choosing the right industrial casters is the key to ensure the efficient movement and safe operation of equipment.
I. Smooth ground scenario:
In smooth floor scenarios, the main task of industrial casters is to provide low friction and smooth movement. Common smooth floors include indoor floors, concrete floors, etc. For such scenes, it is recommended to choose industrial casters with the following characteristics:
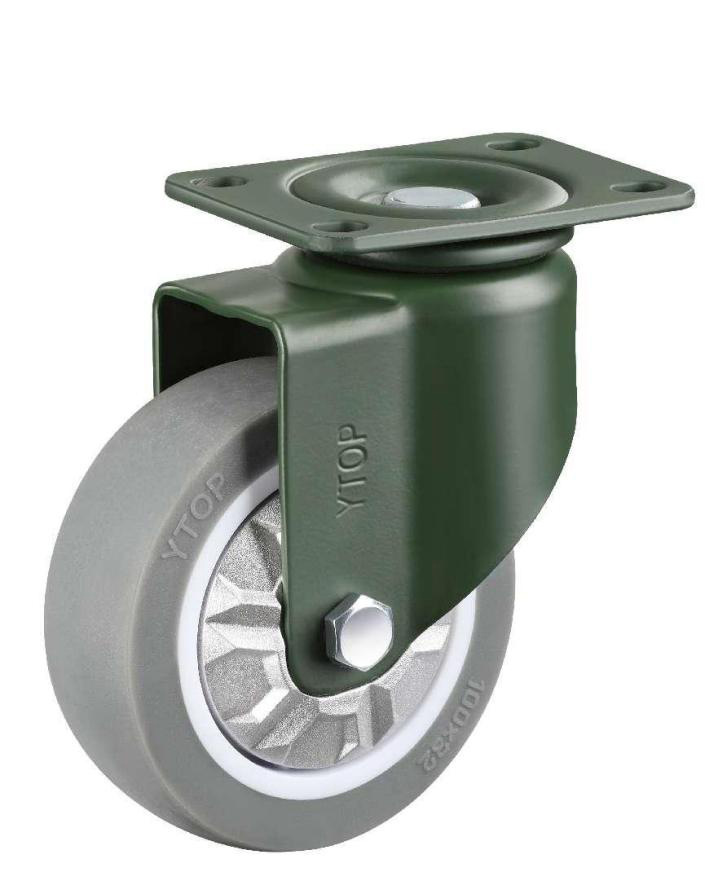
Low friction: Choose casters made of hard materials, such as polyurethane or rubber. These materials have a low coefficient of friction, which reduces resistance when pushing or pulling equipment and improves movement efficiency.
Quiet operation: In order to keep the indoor environment quiet, industrial casters with shock absorption and cushioning effect should be selected. Rubber and polyurethane casters can effectively reduce ground vibration and noise.
II. Unsmooth ground scenario:
In the unsmooth ground scenario, industrial casters need to deal with the challenges of uneven ground and granular materials. Common unsmooth ground includes poorly paved ground, earthy ground and construction sites, etc. For this scenario, it is recommended to choose industrial casters with the following characteristics:
Abrasion resistance: Choose a caster material with abrasion resistance, such as those made of nylon. These materials can withstand greater impact and friction on uneven ground, extending the service life of casters
High load capacity: Considering the challenges of uneven ground, choose industrial casters with high load capacity. This will ensure that the equipment remains stable under heavy loads or uneven ground and avoid accidents.
Adaptability: Industrial casters should have the ability to adapt to different ground surfaces. Casters with adjustable height or swivel can be selected to adjust to the ground conditions and ensure smooth movement of the equipment.
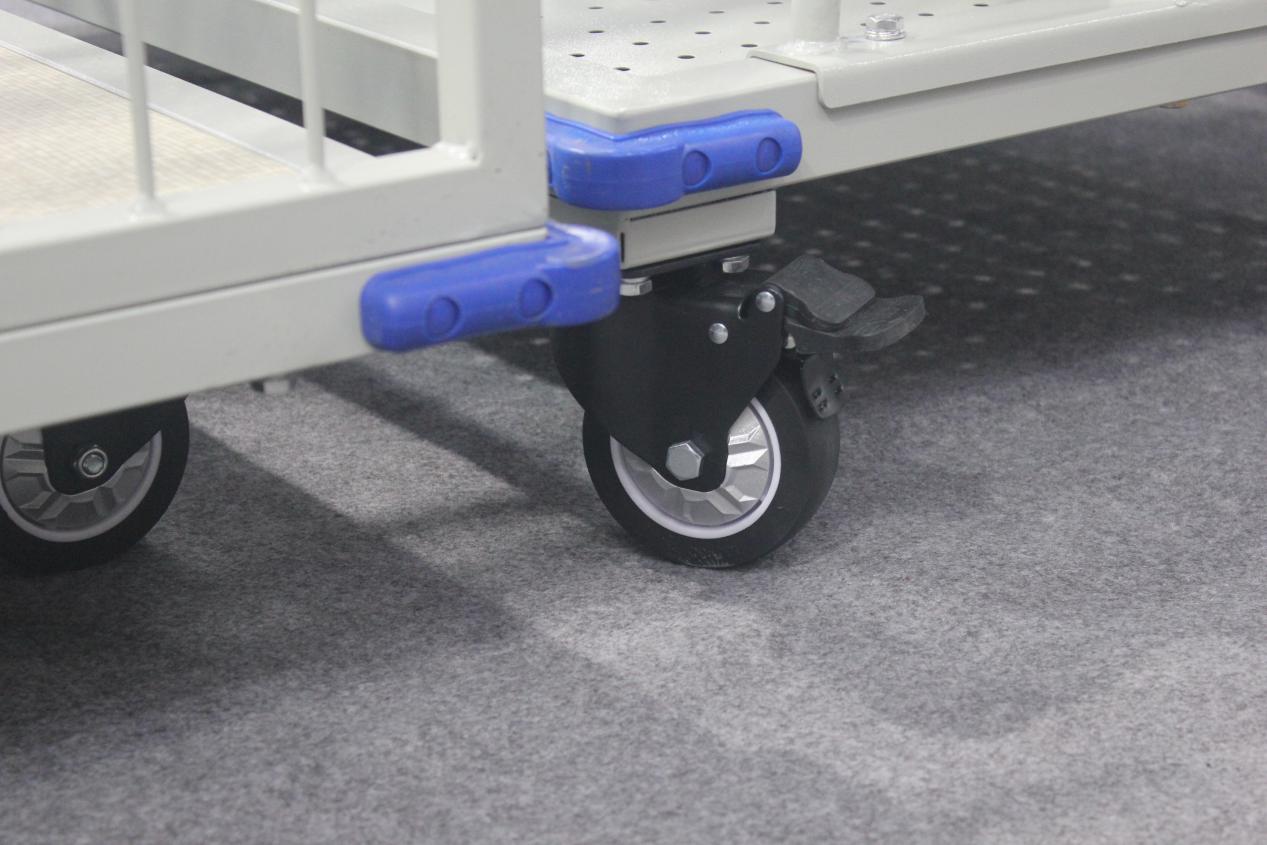
III. High-temperature or chemical environment scenarios:
In high-temperature or chemical environment scenarios, industrial casters need to be able to resist high temperatures, corrosion and chemical attack. Common high-temperature or chemical environments include stoves, chemical plants, laboratories, etc. For such scenarios, it is recommended to choose an industrial caster with the following characteristics:
High temperature resistance: Choose casters that can work in high temperature environments, such as high temperature polyimide or high temperature resistant metal materials. These materials have good heat resistance and can maintain the performance and stability of casters in high temperature environments.
Corrosion resistance: In a chemical environment, choose caster materials that can resist corrosion, such as stainless steel or chemically inert materials. These materials can prevent the erosion of chemical substances on casters and extend the service life.
Anti-static capability: In scenarios such as laboratories or electronic manufacturing, choose casters with anti-static features to avoid damage to equipment or products from static electricity.
Post time: Jul-03-2023